Track treatment fleet
Our machines look after the tracks to keep trains running smoothly and safely
We work around the clock in all weathers, to keep the railway running and our fleet of machines and vehicles help to make this happen. We have various machines that help to prevent the risk of trains derailing and ensure smooth, comfortable journeys for passengers and freight trains. These machines generally work at night when no passenger trains are running.
Jump to
Grinding trains
A grinding train maintains the track and helps to increase the lifespan of the rail. These trains remove small layers of metal from the railhead, helping us to keep the track in good condition.
Our new fleet was introduced in 2017 and offers increased metal removal due to more productive grinding at speeds of up to 15mph. The machines are modular, therefore can be attached together to make a larger machine or stay small to be more targeted.
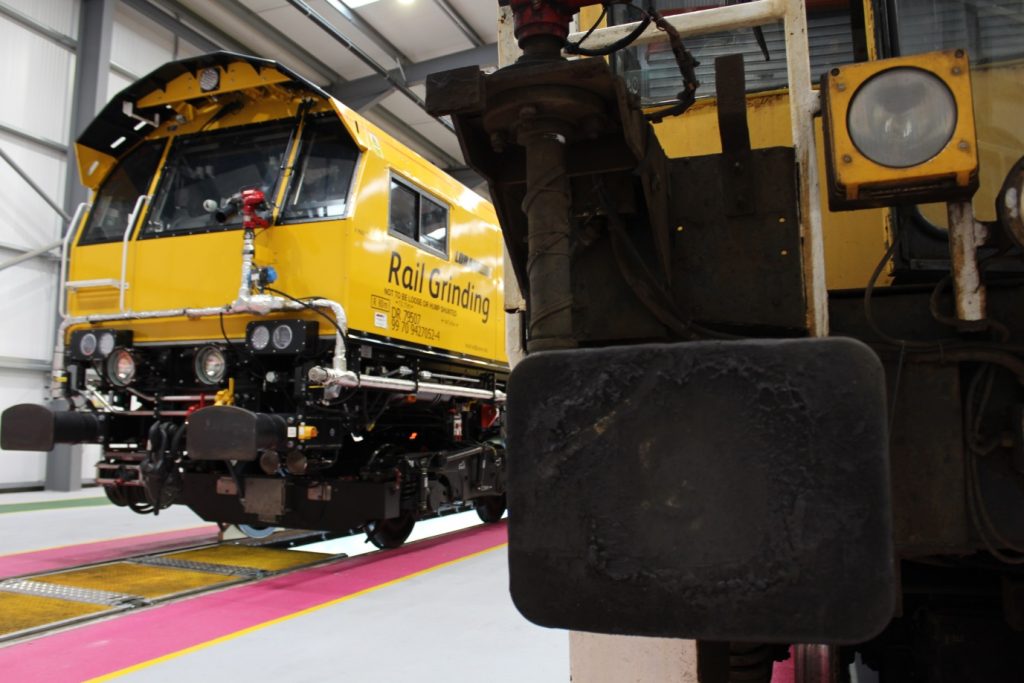
Stoneblowers
Stoneblowers restore the line and level of the track by correcting its vertical (height) and lateral (left or right) profile. To do this, first they measure the track to work out where it needs to be lifted to bring it level, and how much it needs to be moved side to side to ensure correct alignment.
Tampers and stoneblowers are track maintenance machines that make sure the track is correctly aligned and has a smooth level along the rail. They help to prevent the risk of trains derailing, and ensure smooth, comfortable journeys for passengers and freight trains. These machines generally work at night when no passenger trains are running.
After the measurement run, the machine moves along the track, lifting it up at each sleeper and using compressed air to blow extra stones under the sleeper where required to level it up. This tends to give a more durable result than using a tamper, and so can extend the life of the track by many years, saving the railway significant amounts of money. Given their specialist nature, all the stoneblowers are owned by Network Rail.
Did you know?
- Although most of the stoneblower fleet works only on plain line (straight) track, there are three multipurpose stoneblowers, which also work on points and crossings.
- We developed these jointly with machine manufacturer Harsco Rail.
- The multipurpose stoneblowers are the only three machines of their type in the world.
- They have been so successful at extending the life of old points and crossings that we’re looking at buying more to replace the old and life-expired plain line stoneblower machines.
Numbers of these machines in operation:
Plain line – 11
Multipurpose – 3
Click the arrows on the images to browse the gallery below.
Tamping
Tamping machines do the same job as stoneblowers, restoring the line and level of the track, but work in a slightly different way.
They insert large tools called tines into the ballast – the stones beneath the track – and then force the tines together to move ballast under the sleepers. The tamping machine moves additional ballast under the sleepers to raise the height of the track and can move the track sideways if required.
It is programmed with geometrical data that shows where the track should be, and compares the data with the actual track position using on-board measuring equipment. The machine then calculates the required movements to reposition the track according to the geometrical data.
Some tamping machines can be used to treat switches and crossings (S&C), while others are for treating plain line (straight) track.
We currently contract around 65 tamping machines nationally from the following suppliers:
Click the arrows on the images to browse the gallery below.
Dynamic Track Stabilisation and high-speed handbacks
Dynamic Track Stabilisation (DTS) units are available on some of the more advanced tampers of the type you can see on this page, as well as High Output tampers.
When a tamper is used alone to place the track in its design position and consolidate the ballast after renewal work, there is traditionally a line speed restriction of around 50mph for a period of time afterwards to allow the ballast to settle.
When DTS machines are used together with a tamper, their impact is to consolidate the ballast by simulating the equivalent of up to a week’s worth of trains, so the track won’t settle further. The result is that trains can run on the track at high speeds (80-125mph) straight after renewal work. This is called a high-speed handback.
The video below and the images above are of DTS units on SB Rail tampers during a shift with the Switches & Crossings (S&C) North Alliance Doncaster team in October 2017. The team delivered 115mph handback on an S&C track renewal at High Dyke.
Ballast regulators
Regulators are used to correct the track’s ballast profile by redistributing ballast to the right areas of the ballast bed (beneath the track) to give the track lateral stability. The even bed of stone prevents the track from moving when under the load of a train.
We currently contract six regulators from the following suppliers:
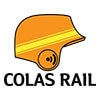
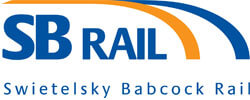
