The autumn is the most challenging time of year for the railway, so we spend the rest of the year preparing for it at our maintenance depot.
Millions of trees grow alongside the railway, dropping thousands of tonnes of leaves onto the tracks throughout the season.
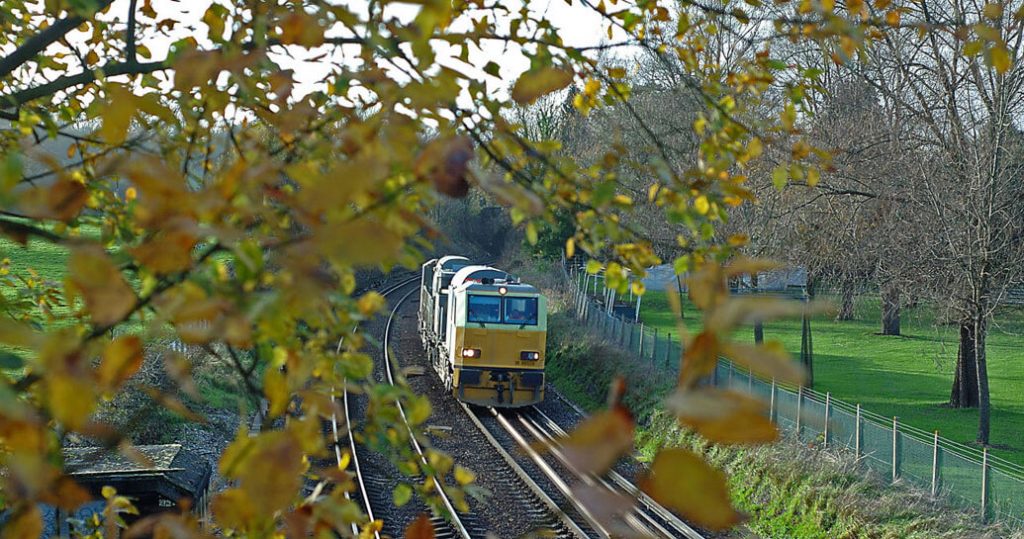
Leaves on the line can cause delays by sticking to damp rails. Passing trains compress them into a thin, black layer on the rail which – much like black ice on the roads – affecting braking and acceleration.
This means train drivers must slow down earlier for stations and signals to avoid overshooting them. They must also accelerate more gently to avoid wheel spin. All this can increase journey time and lead to delays for passengers.
Build-up of leaf mulch can also make it harder for our signallers to detect a train’s location, causing delays when subsequent trains are unable to proceed until the train in front moves further up the line.
Our leaf-busting trains clean the rails with jets of water and lay adhesion modifier – a mixture of suspension gel, sand and steel or iron shot – on the rails to aid traction and help trains run normally.
Holgate – our fleet maintenance depot
Seasonal track treatment is a huge operation. That’s why for most of the year we maintain our fleet of leaf-busting trains at our massive depot, Holgate Engineering Works in York.
Holgate is our largest depot at 24 acres in total, including its 12-acre maintenance building. The vast facility houses equipment including track, workshops, sidings, cranes, and switches – the movable sections of track that guide trains from one track to another. Other trains we maintain here include rail delivery train and rail grinders.
We prepare 61 specialist autumn trains and vehicles at Holgate to minimise the impact of leaf fall. These multi-purpose vehicles (MPV) and railhead treatment trains (RHTT) are decommissioned for maintenance after each autumn – all the water and adhesion modifier is drained and the pipe work removed so they can be dismantled.
The trains then get a full service at Holgate, where we wash them and replace any faulty parts. We then test the vehicles before they travel across Britain.
Click on the gallery to see Holgate and RHTTs at the depot preparing to travel across the network
Doing the rounds
Once deployed from Holgate for the season, MPVs operate out of nine locations across Britain and RHTTs from a further 15. Both types return to their base after each shift for maintenance and refilling, having travelled around much of their part of the rail network in one night.
Executing the vital work of driving the vehicles are leaf-busting teams who are available 24 hours a day, seven days a week during the autumn.
We inspect the vehicles daily to make sure they’re safe to operate before every night shift. Preparation includes replenishment of water, diesel and adhesion modifier.
One of our MPVs and track treatment in action
Autumn treatment in numbers:
- Our rail head treatment trains hold 17,000 litres of water – the same as more than 200 bathtubs.
- In 2017, our seasonal fleet covered about 1.7 million miles – equivalent to travelling to the moon and back 3.5 times.
- Our planned visits to sites on the railway requiring autumn treatment have doubled in a decade to almost 360,000.
- We lay two litres of adhesion modifier a minute at 60mph.
- An adhesion modifier tank holds about 1,000 litres – the same as the water in a small fire engine.