A high-speed milling train took to our railway for the first time this week, providing quadruple the capacity to treat rail head defects.
The HSM-R-B rail milling train carried out its first shift, in Herne Bay, Kent, on 26 June. The train, which Network Rail is leasing for two years, replaces the Strabag SF-02 road-rail milling machine decommissioned in December.
It targets defects in the rail head by removing a layer of its metal. This leaves a clean running surface to profile, and improves safety and train dynamics. The result is smoother journeys, without the need to close the railway during track replacements.
High output
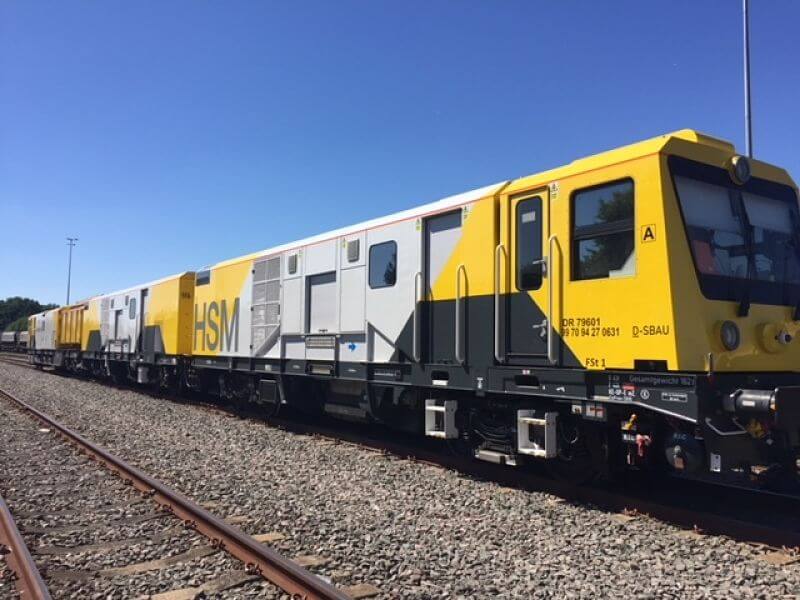
The new train, built by Schweerbau, is a first for Network Rail, which has previously used road-rail vehicles for the job. The HSM-R-B has two milling heads per rail, per train, and is considerably larger than road-rail vehicles. It will be run as a duplex unit, providing capacity for four milling heads per rail. This means it can treat four times the amount of rail a road-rail vehicle could in one night. Its high speed refers to the amount it can mill – about 1.5km an hour.
Leevan Finney, director, fleet and engineering, Route Services at Network Rail, said: “Each train that runs on the network causes an element of wear and tear, and in some cases damage to our rails.
“Since 2002, Network Rail has implemented a process of frequent rail grinding which removes small amounts of metal from the rail surface to maintain the profile – the portion of the track which comes in to contact with the train wheel.”
Each year, Network Rail grinds more than 5,000 miles of track and more than 3,000 switch units to remove defects and maintain a smooth rolling surface for trains. Passing trains and exposure to the elements can cause cracks; a severe crack not addressed in time can break the rail, leading to potential derailments.
Leevan said: “With milling we can get out to the site, treat the profile and go back to the base all in one shift. All metal removed from the rail will be returned and recycled, too.”
Increased safety
The train features an automated system for changing milling tools, improving safety by reducing the need for colleagues working trackside.
Bob Kingman, manager, principal fleet engineering, Route Services, said: “With the new [leased] milling train there is a huge drop in decibel levels for operation compared to most services, which is better for people living by the railway; it’s also faster, cleaner and produces less waste.
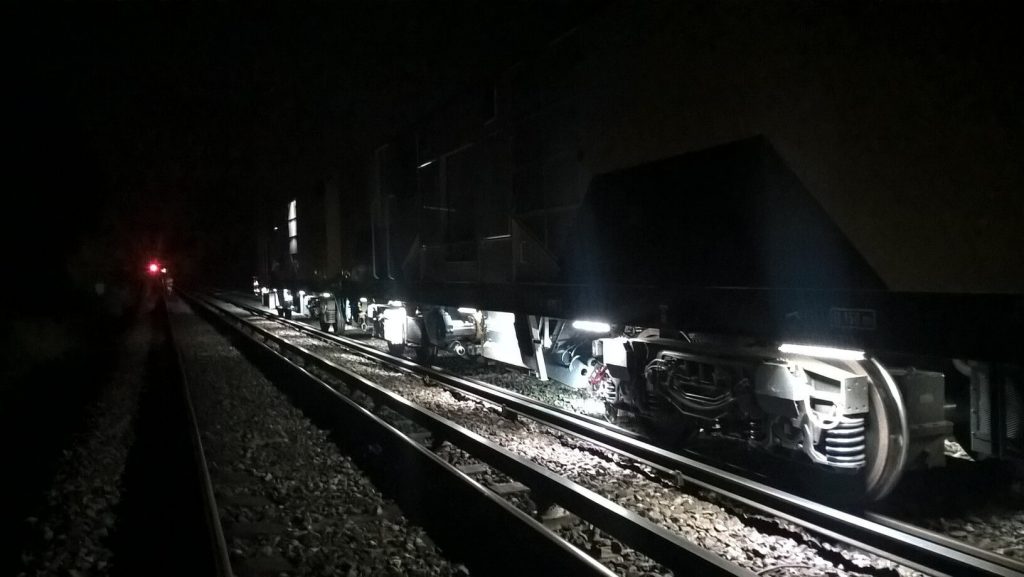
“We always consider the environmental impact before a new machine joins our fleet, looking at the latest standards to ensure it meets these as a minimum.”
Network Rail will use the machine until its new, owned milling train joins the Supply Chain Operations stable. This is in the design stage and will be made by Linsinger, due to join Network Rail’s fleet in 2020 or 2021. The new machine will build on lessons from the grinding train introduction, offering innovation for the network.