We have 20,000 miles of track, which means we have a lot of steel rail.
With demand for train travel doubling in the past 20 years, its maintenance and renewal keep us busier than ever.
Our engineers are always improving how we look after the railway. With rail, this means trying our best to prevent problems like broken or buckled rail before they arise and ensuring it’s safe for passenger and freight trains.
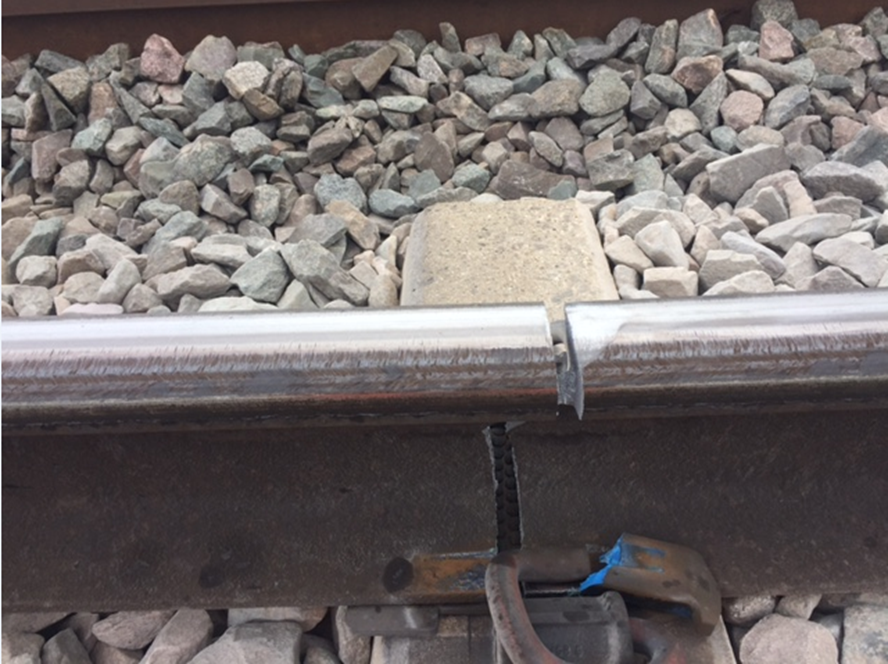
How do these problems happen and how do we try to stop them?
On average, we record about 100 broken rails a year – a huge decrease from 20 years ago, when we recorded more than 900 in one year. Broken rail incidents exceeding 700 a year were typical in the 1980s while figures of 600 and up were common in the 1990s.
Achievements in reducing the number of broken rails each year have come despite a surge in rail travel – and less access to track for our engineers.
Broken rails can occur because of a small defect in the rail or where the rail is subject to excessive loads. Small defects can grow under repetitive loading – more than three million axles (part of a wheel) pass over the rail every year on a busy mainline.
Imagine a wire coat hanger – you can bend it but if you do that too much, you’ll weaken the metal. It’s the same principle with rail – it has a certain amount of strength and ductility. Some of the rail strength is used during cold weather as the rail is under tension as it is stressed to prevent it buckling during hot weather.
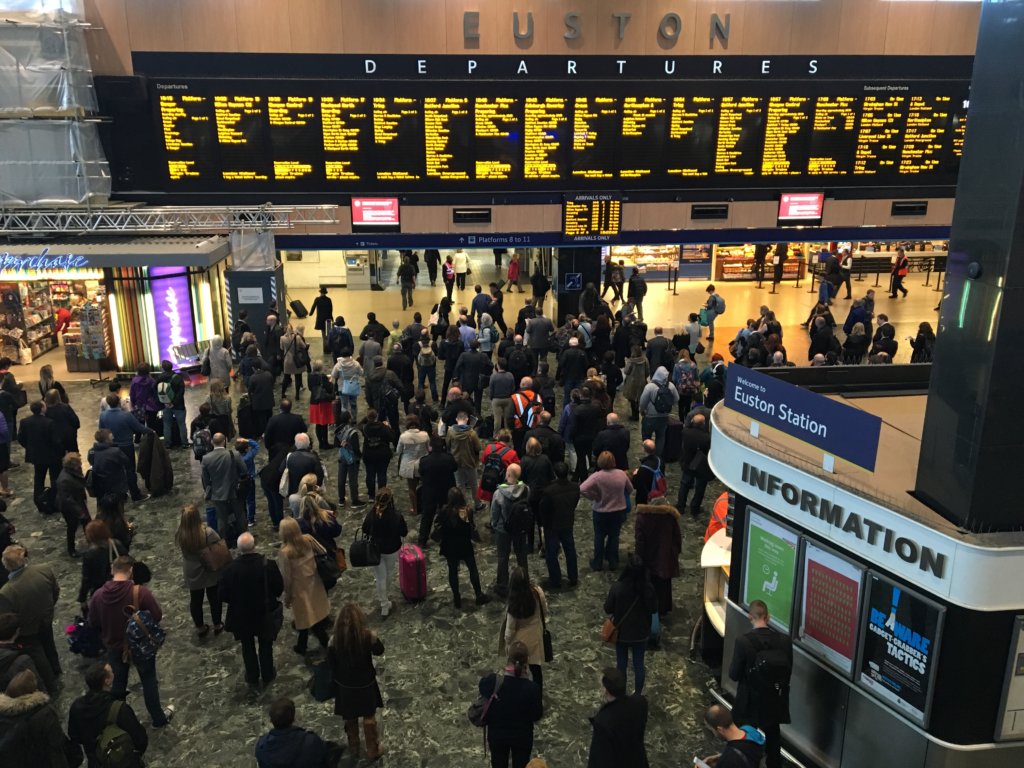
Stressing is required to enable the rail to cope with different temperatures in different seasons. Due to the high forces exerted on the rail in service defects need to be identified and removed before they reach a critical size and the rail is at risk of failure.
Why do we stress rails?
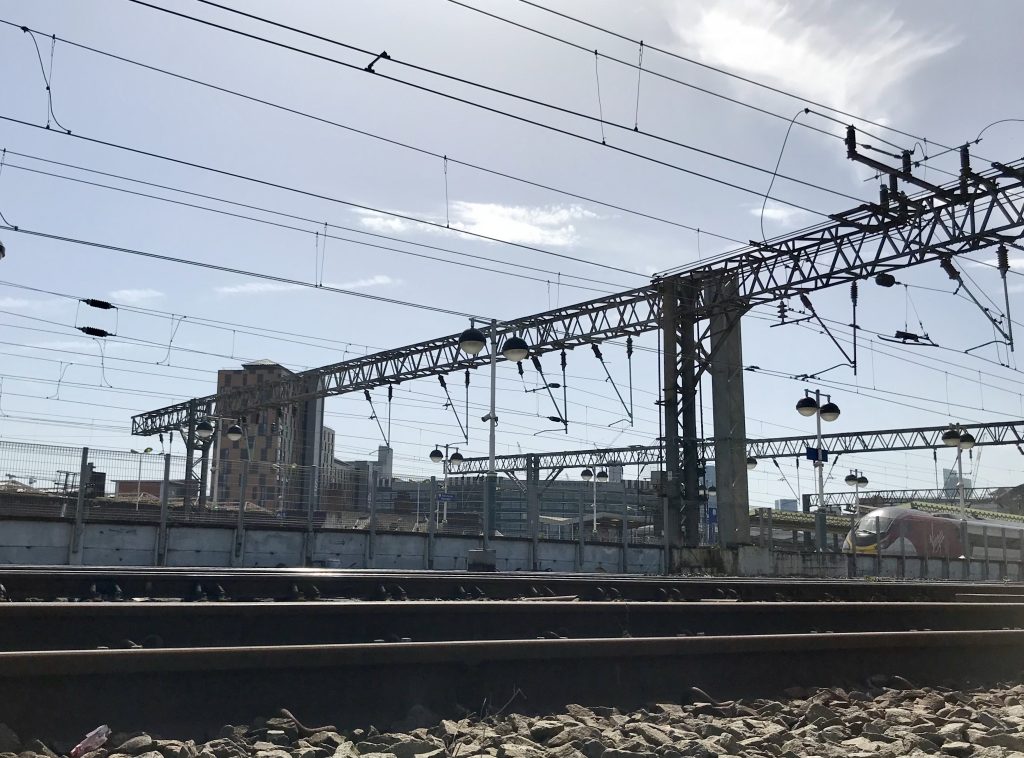
In engineering terms, stressing is a good thing – it helps us keep the railway safe in very hot or very cold temperatures.
In case a British summer features abnormally high temperatures, we must plan for intense heat, which can cause rails to expand. Where the compressive forces in the rail reach a critical point, the track can suddenly distort sideways, causing a buckle if it is not restrained sufficiently by the ballast around the sleepers. Read more about why we stress rails to prepare for hot summers.
If we plan to stress rails, why do rails sometimes break?
We work hard to keep a close eye on the entire railway but sometimes, incidents happen. Usually, it’s because something has unfortunately failed in our process.
We investigate the incident and ask why it happened and how we could change our processes to prevent it from happening again.
How do we fix a broken rail?
In simple cases, we can clamp a broken rail and tell trains to slow down – known as a temporary speed restriction – until we can send engineers to fix the problem permanently. This limits disruption to passengers. However, it’s not always possible to do this – for instance, if the break is too big or at an angle and cannot be safely clamped.
A broken rail on a straight piece of track – known as a plain line – is easier to fix because it’s simple to replace a with a short length of new rail.
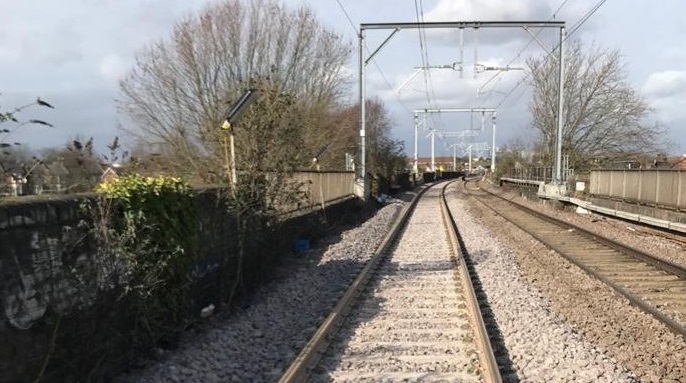
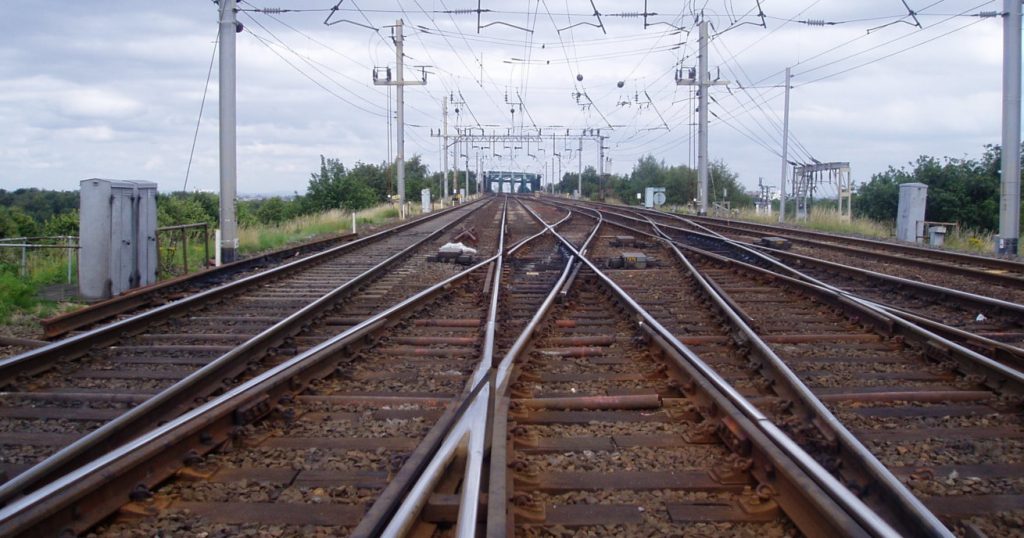
It’s usually the location of the rail that makes it more difficult to repair – parts of railway like switches and crossings have been built with bespoke machined rail or specifically designed cast crossings. This is rail specifically designed and manufactured for that precise location.
Why? First, because some places have more complicated sections of track in junctions. Second, because much of our railway is old and designs have been changed over time to improve reliability and performance.
This means we can easily and quickly fetch a replacement piece of rail for plain line track but we must often manufacturer a replacement for bespoke track, which takes time.
Gallery: Our special Road Rail Vehicle (RRV) fixing broken rail and welding new rail
If a rail breaks on one line, why does it delay trains on the lines next to it?
We know delays are frustrating and we do everything we can to avoid them but we must always balance risk.
Safety is paramount – when we send our teams out to track to repair a piece of rail, we must create a safe environment around them. Increasingly, this means giving them more space around the line they’re working on, which may require speed restrictions on adjacent lines.
For complex switches and crossings, a broken rail may affect multiple lines, preventing trains from passing from one track to another.
How are we improving?
As well as improving our processes for safety, we’re working towards a more standardised railway so that in future, we will be able to run a railway with far fewer bespoke sections of track.
This would mean we could potentially use 3D printing to make replacement components as and when we need it – something that’s expected to become more common in the automotive and aerospace sectors.
We currently keep a certain amount of spare rail and switches and crossings components for repairs but Britain’s railway has 20,000 miles of track and more than 19,000 junctions so we can’t keep spares for every part of it.
Meanwhile, we’re significantly improving the technology we use to monitor the condition of rail across the country. One of the things we do is ultrasonically test rail – big yellow trains fitted with complex test equipment that emit high frequency sound into the rail at different angles to look for small cracks inside the rail.
We also use Plain Line Pattern Recognition Technology (PLPR) in combination with track geometry measurement, which dramatically increases our capacity to monitor, inspect and fix track faults by analysing high definition imagery of the rails, fastenings, sleepers and ballast.
Read more about PLPR and watch this video to find out more: